目前,上至中央下至各省市,都將“環(huán)境質(zhì)量改善”作為環(huán)保工作的核心,把“總量減排”作為主要手段。對(duì)于水泥行業(yè)來(lái)說(shuō),無(wú)論是百年老企,還是小型廠家,都力爭(zhēng)在環(huán)保的高壓態(tài)勢(shì)下達(dá)到符合各項(xiàng)指標(biāo)的排放標(biāo)準(zhǔn)。
此時(shí),分級(jí)燃燒、SNCR等各項(xiàng)脫硝技術(shù)紛紛涌現(xiàn),其中SNCR脫硝技術(shù)運(yùn)用尿素、氨水、催化劑等物質(zhì),雖可實(shí)現(xiàn)水泥企業(yè)的良好脫硝效果,但后期運(yùn)行成本過(guò)高。分級(jí)燃燒技術(shù)雖無(wú)后期運(yùn)行成本,但脫硝效果不夠理想。在各項(xiàng)脫硝技術(shù)皆有弊端之時(shí),亟需出現(xiàn)脫硝效果良好及運(yùn)行成本低的脫硝技術(shù),備受矚目的無(wú)氨脫硝技術(shù)成為引*水泥行業(yè)的環(huán)保風(fēng)向標(biāo)。
河南匯金智能裝備研發(fā)的HJ無(wú)氨脫硝窯尾燒成系統(tǒng)是以多條新型干法水泥生產(chǎn)線實(shí)際窯尾燒成系統(tǒng)的技術(shù)分析為依據(jù),采用計(jì)算機(jī)數(shù)值模擬仿真技術(shù)對(duì)新型干法回轉(zhuǎn)窯及分解爐中煤粉的燃燒規(guī)律和分解規(guī)律進(jìn)行仿真優(yōu)化計(jì)算,采用分解爐高強(qiáng)還原燃燒控制技術(shù),使煤粉在分解爐內(nèi)全部分解,形成大量的CO、CHi、H2、HCN和固定碳等還原劑,將窯內(nèi)產(chǎn)生的熱力型NOX強(qiáng)力還原成N2。從而大幅度減少窯尾煙氣的NOX含量,達(dá)到脫硝的目的。
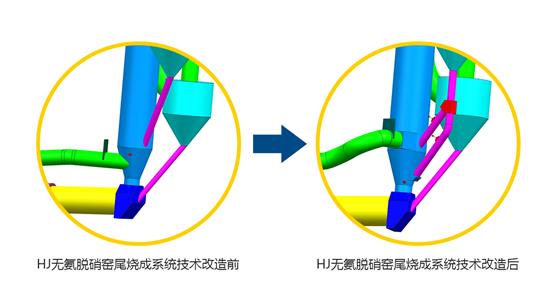
HJ無(wú)氨脫硝窯尾燒成系統(tǒng)技改前、后對(duì)比示意圖
HJ無(wú)氨脫硝窯尾燒成系統(tǒng)以先進(jìn)的脫硝技術(shù)為根基,對(duì)水泥生產(chǎn)線進(jìn)行技術(shù)改造。具體方案如下:四級(jí)旋風(fēng)筒下料管對(duì)分解爐下料點(diǎn)位于三次風(fēng)管之上,高于三次風(fēng)管0.5米以上。將每列單管下料更改為雙管下料,每單列增加一套分料閥、翻板閥、撒料箱及相應(yīng)的下料管延長(zhǎng)。三次風(fēng)管的位置在三次風(fēng)管與窯尾煙室縮口之間形成的強(qiáng)力還原區(qū)的上部。
經(jīng)HJ無(wú)氨脫硝窯尾燒成系統(tǒng)脫硝技改后的諸多水泥生產(chǎn)線,皆達(dá)到了“可在不增加成本、增強(qiáng)水泥煅燒性能的前提下,NOX排放濃度大幅度降低,降低氨水用量60%以上”的效果,滿足了水泥企業(yè)在生產(chǎn)過(guò)程中的環(huán)保要求。同時(shí),還可大幅度節(jié)約煤耗、提高產(chǎn)量,且能適應(yīng)煤質(zhì)的變化,可解決低劣及高硫煤資源在新型干法水泥工業(yè)中的應(yīng)用問(wèn)題,降低一定的生產(chǎn)成本。
現(xiàn)匯金智能裝備已在水泥行業(yè)留下了眾多*工程,以山西某大型企業(yè)3200T/D生產(chǎn)線為例,自啟用匯金智能裝備無(wú)氨脫硝窯尾燒成系統(tǒng)脫硝技改以來(lái),氨水用量從0.5m3/h降至0.2m3/h,實(shí)際節(jié)約0.3m3/h,節(jié)約氨水效果高達(dá)60%。具體技術(shù)參數(shù)對(duì)比表詳見如下:
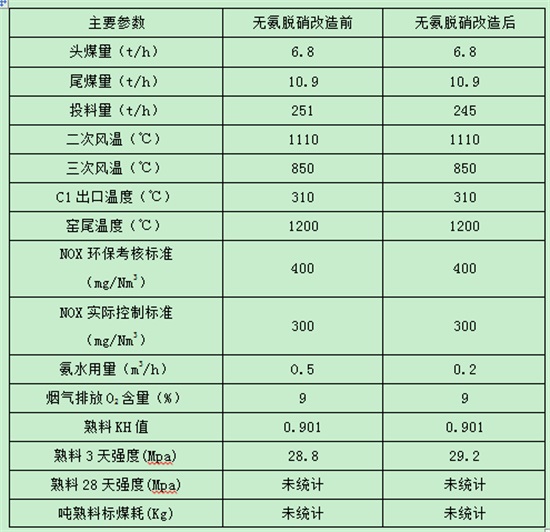
水泥行業(yè)的排放標(biāo)準(zhǔn)將不斷收緊,早已在水泥行業(yè)成為共識(shí)。無(wú)氨脫硝作為水泥行業(yè)的脫硝佼佼者,定能逐步提升市場(chǎng)份額,成為水泥行業(yè)的環(huán)保趨勢(shì)。匯金智能裝備作為無(wú)氨脫硝技術(shù)的掌握者,也將繼續(xù)致力于環(huán)保技術(shù)的研發(fā),為水泥行業(yè)的環(huán)保事業(yè)貢獻(xiàn)更多力量,這是義務(wù)也是責(zé)任。
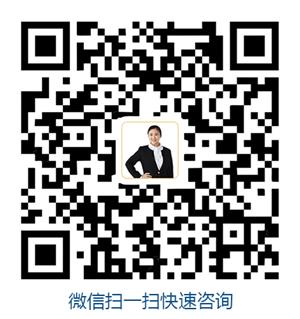