1、前言 隨著環(huán)境保護(hù)工作形勢(shì)的日益嚴(yán)峻,NOx作為重點(diǎn)管控指標(biāo)之一,新型干法水泥回轉(zhuǎn)窯內(nèi)的燒結(jié)溫度高,過(guò)剩空氣量大、NOx排放濃度高且灰量大使其脫硝工程面臨著艱巨的挑戰(zhàn)。目前用于水泥回轉(zhuǎn)窯NOx排放的控制技術(shù)大多采用選擇性非催化還原技術(shù)SNCR,但SNCR技術(shù)脫氮效率低,日常投入費(fèi)用太高,給企業(yè)生產(chǎn)經(jīng)營(yíng)增加了較重的經(jīng)濟(jì)負(fù)擔(dān)。本文介紹了煙氣脫硝窯尾燒成系統(tǒng)優(yōu)化的技術(shù)原理和技術(shù)方案,通過(guò)采用窯尾分解爐高強(qiáng)還原燃燒控制技術(shù)可實(shí)現(xiàn)將回轉(zhuǎn)窯內(nèi)熱力型NOx高強(qiáng)還原,大大降低了NOx生產(chǎn)量,結(jié)合在山東省某水泥集團(tuán)5000噸熟料生產(chǎn)線的實(shí)踐應(yīng)用,實(shí)現(xiàn)了采用煙氣脫硝窯尾燒成系統(tǒng)優(yōu)化后可大大降低NOx本體濃度56%以上,在相同NOx控制指標(biāo)下可節(jié)約氨水用量58%以上,煙氣脫硝窯尾燒成系統(tǒng)優(yōu)化大大降低了NOx排放濃度,降低了氨水用量和脫硝成本,具有顯著的經(jīng)濟(jì)效益和社會(huì)效益。
1、煙氣脫硝窯尾燒成系統(tǒng)技術(shù)原理2.1 煙氣脫硝窯尾燒成系統(tǒng)技術(shù)原理 煙氣脫硝窯尾燒成系統(tǒng)采用分解爐高強(qiáng)還原燃燒控制技術(shù)和窯頭窯尾用煤量?jī)?yōu)化控制技術(shù),使煤粉在分解爐內(nèi)全部分解,形成大量的CO、CHi、H2、HCN和固定碳等還原劑,將窯內(nèi)產(chǎn)生的熱力型NOx強(qiáng)力還原成N
2,從而大幅度減少窯尾煙氣的NOx含量,降低NOx的本體濃度,達(dá)到脫硝的目的。
2.2 煙氣脫硝窯尾燒成系統(tǒng)優(yōu)化原則 煙氣脫硝窯尾燒成系統(tǒng)優(yōu)化在降低NOx本體濃度的同時(shí),通過(guò)對(duì)分解爐燃燒器、三次風(fēng)管、四級(jí)下料點(diǎn)在分解爐分布系統(tǒng)的優(yōu)化,實(shí)現(xiàn)了分解爐內(nèi)風(fēng)、煤、料的混合均勻分布,避免分解爐內(nèi)局部高溫,優(yōu)化分解爐內(nèi)的熱工分布制度,還原回轉(zhuǎn)窯內(nèi)的NOx生成量,減少分解爐內(nèi)燃料型NOx的生成量。其中對(duì)分解爐燃燒器、三次風(fēng)管、四級(jí)下料點(diǎn)的優(yōu)化原則如下:
(1)煙氣脫硝窯尾燒成系統(tǒng)優(yōu)化對(duì)分解爐燃燒器的優(yōu)化原則是高固氣比煤粉輸送技術(shù);保證煤粉入分解爐分散效果;保證煤粉入分解爐的覆蓋區(qū)域和停留時(shí)間。
(2)煙氣脫硝窯尾燒成系統(tǒng)優(yōu)化對(duì)三次風(fēng)管的優(yōu)化原則是保證脫硝效果的同時(shí)保證煤粉完全燃燒;即保證還原劑與NOx的還原反應(yīng)時(shí)間;同時(shí)保證三次風(fēng)在分解爐內(nèi)的停留時(shí)間,保證煤粉的完全燃燒。
(3)煙氣脫硝窯尾燒成系統(tǒng)優(yōu)化對(duì)四級(jí)下料點(diǎn)的優(yōu)化原則是保證分解爐內(nèi)不產(chǎn)生局部高溫;保證分解爐內(nèi)不結(jié)皮;保證下料管不結(jié)皮堵塞;保證不塌料。
3、煙氣脫硝窯尾燒成系統(tǒng)優(yōu)化技術(shù)方案 山東省某水泥集團(tuán)5000噸熟料生產(chǎn)線是南京設(shè)計(jì)院設(shè)計(jì)5000噸/天熟料生產(chǎn)線,熟料實(shí)際產(chǎn)量5800噸/天,標(biāo)準(zhǔn)煤耗102kg/t熟料,現(xiàn)有脫硝系統(tǒng)采用選擇性非催化還原技術(shù)SNCR,NOx控制在150mg/m
3以內(nèi),氨水平均用量在700kg/h。窯系統(tǒng)存在SNCR技術(shù)脫硝效率低,氨水用量偏大,煤耗偏高,日常投入環(huán)保費(fèi)用偏高。2021年2月我公司進(jìn)行了煙氣脫硝窯尾燒成系統(tǒng)優(yōu)化的技術(shù)改造,技術(shù)改造的前提是保證現(xiàn)有熟料產(chǎn)質(zhì)量,優(yōu)化窯況工藝參數(shù),技術(shù)改造的目的是降低NOx的本體濃度,節(jié)約SNCR氨水用量。煙氣脫硝窯尾燒成系統(tǒng)優(yōu)化方案如下:
3.1 生產(chǎn)現(xiàn)狀和主要工藝參數(shù)
(1)煙氣脫硝主要技術(shù)指標(biāo)
設(shè)計(jì)院 |
南京水泥設(shè)計(jì)院 |
分解爐型號(hào)規(guī)格 |
Φ7.3m×31.7m |
設(shè)計(jì)產(chǎn)量(T/D) |
5000 |
實(shí)際產(chǎn)量(T/D) |
5800 |
煙室縮口尺寸 |
Φ2150mm |
NOx(SNCR前)(mg/Nm3) |
800-830 |
NOx(SNCR運(yùn)行實(shí)際)( mg/Nm3) |
130±20 |
SNCR氨水用量(kg/h) |
700 |
NOx環(huán)??己藰?biāo)準(zhǔn)( mg/Nm3) |
320以內(nèi) |
煙氣排放 O2含量(%) |
9.63 |
煙氣排放 CO 含量(%) |
0.013 |
(2)窯況主要工藝參數(shù)
頭煤量(t/h) |
尾煤量(t/h) |
投料量(t/h) |
二次風(fēng)溫(℃) |
三次風(fēng)溫(℃) |
煙室溫度(℃) |
分解爐溫度(℃) |
C1筒溫度(℃) |
|
11.5 |
22 |
380 |
1030±20 |
850 |
1050±20 |
880 |
325 |
|
生熟料化學(xué)成分分析(%) |
|
|
LOSS |
SiO2 |
Al2O3 |
Fe2O3 |
CaO |
MgO |
K2O |
Na2O |
SO3 |
生料 |
35.61 |
13.18 |
3.23 |
1.99 |
42.68 |
1.16 |
0.70 |
0.13 |
0.26 |
熟料 |
0.20 |
31.38 |
5.56 |
3.07 |
65.20 |
1.70 |
0.88 |
0.14 |
0.75 |
煤粉工業(yè)分析 |
|
灰分(A) |
揮發(fā)分(V) |
熱值(KC/KG) |
細(xì)度(N) |
固定碳(C) |
水份(M) |
硫含量(%) |
氮含量(%) |
|
21.28 |
29.40 |
5600 |
11±1 |
51.8 |
1.67 |
- |
- |
|
(3)窯尾送煤風(fēng)機(jī)配置參數(shù)
風(fēng)機(jī) |
功率(KW) |
流量(m3/min) |
壓力(Kpa) |
窯尾送煤風(fēng)機(jī) |
160 |
105 |
68.6 |
3.2分解爐窯尾燃燒器優(yōu)化方案
(1)窯尾送煤風(fēng)機(jī)參數(shù)優(yōu)化
采用高固氣比煤粉輸送技術(shù),采用變頻調(diào)節(jié)減少入分解爐冷風(fēng)量,一方面可以節(jié)約熟料煤耗,同時(shí)冷風(fēng)量的減少使氧氣的帶入量降低,有利于還原區(qū)的創(chuàng)建。具體使用運(yùn)行參數(shù):流量:60m3/min;壓力:25-30kpa;功率:90kw。
(2)窯尾送煤管道的優(yōu)化
窯尾送煤主路管道改為外徑ф245mm(內(nèi)徑ф229),一分二路送煤管道改為ф180mm(內(nèi)徑ф164),二分四路送煤管道改為ф146mm(內(nèi)徑ф130)。送煤管道的優(yōu)化是獲得最佳的固氣比,穩(wěn)定送煤氣流,保證送煤量的均勻穩(wěn)定,有利于分解爐溫度環(huán)境的穩(wěn)定,可獲得均勻穩(wěn)定的NOx還原區(qū)。
(3)分解爐燃燒器和位置的優(yōu)化
更換旋流擴(kuò)散型分解爐燃燒器,由原來(lái)的兩點(diǎn)送煤優(yōu)化為四點(diǎn)送煤,安裝位置由原來(lái)的三次風(fēng)管位置處送煤優(yōu)化在分解爐縮口上方1米位置,即優(yōu)化后在分解爐縮口上方1米水平位置均布四個(gè)旋流擴(kuò)散型分解爐燃燒器。如圖1所示為旋流擴(kuò)散型分解爐燃燒示意圖;如圖2所示為優(yōu)化后分解爐燃燒器安裝位置圖。
3.3 三次風(fēng)管優(yōu)化方案
優(yōu)化三次風(fēng)管入分解爐位置,將現(xiàn)有三次風(fēng)管在分解爐錐部位置處提高3.5米,提高到分解爐柱體位置處,便于還原區(qū)的創(chuàng)建。
如圖3所示為原三次風(fēng)管位置示意圖;如圖4所示為優(yōu)化后三次風(fēng)管位置示意圖。
3.4 C4下料管及下料點(diǎn)優(yōu)化方案
優(yōu)化C4下料管和四級(jí)下料點(diǎn),將現(xiàn)有C4雙系列單管下料優(yōu)化為雙系列雙管下料,對(duì)C4上、下料比例進(jìn)行調(diào)整,將C4下料管下部下料點(diǎn)優(yōu)化在分解爐錐部位置并安裝撒料板,C4下料管上部下料點(diǎn)優(yōu)化到新三次風(fēng)管上方并安裝撒料板。如圖5所示為原四級(jí)下料管示意圖;如圖6所示為優(yōu)化后四級(jí)下料管示意圖:
3.5 煙氣脫硝窯尾燒成系統(tǒng)改造工程圖
(1)煙氣脫硝窯尾燒成系統(tǒng)改造安裝總工程圖如圖7所示:

(2)三次風(fēng)管安裝工程圖如圖8所示:
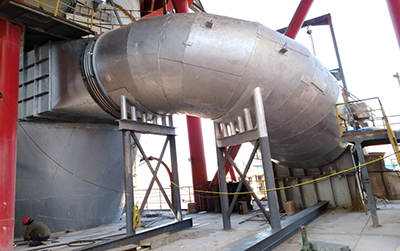
(3)四級(jí)下料管安裝工程圖如圖9所示:
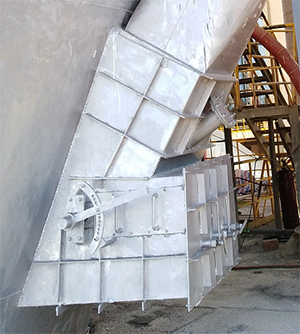
(4)分解爐燃燒器安裝工程圖如圖10所示:
4、煙氣脫硝窯尾燒成系統(tǒng)優(yōu)化實(shí)踐應(yīng)用及效果
4.1 煙氣脫硝窯尾燒成系統(tǒng)優(yōu)化實(shí)施方案
依照煙氣脫硝窯尾燒成系統(tǒng)優(yōu)化的技術(shù)方案,對(duì)分解爐燃燒器、三次風(fēng)管、四級(jí)下料點(diǎn)在分解爐分布進(jìn)行了優(yōu)化施工,整個(gè)項(xiàng)目改造從項(xiàng)目設(shè)計(jì)、施工監(jiān)理、工藝調(diào)試一體化設(shè)計(jì)方案,項(xiàng)目改造共消耗鋼材近60噸,耐火材料100噸,整個(gè)項(xiàng)目工期20天,其中停窯15天。
4.2 煙氣脫硝窯尾燒成系統(tǒng)優(yōu)化效果
煙氣脫硝窯尾燒成系統(tǒng)優(yōu)化改造完成后,一次投料成功,熟料產(chǎn)質(zhì)、量按預(yù)定投料方案按期達(dá)標(biāo),窯尾分料系統(tǒng)、送煤系統(tǒng)運(yùn)行正常,窯況工藝穩(wěn)定,煙室及分解爐錐部未發(fā)生異常結(jié)皮。
(1)熟料產(chǎn)、質(zhì)量,窯況工藝穩(wěn)定性
優(yōu)化改造前投料量為平均370-380t/h,熟料3天強(qiáng)度平均32Mpa,優(yōu)化改造后投料量平均380-390t/h,熟料3天強(qiáng)度平均32Mpa,煙氣脫硝優(yōu)化改造前后熟料產(chǎn)、質(zhì)量不受影響。優(yōu)化改造后窯況工藝穩(wěn)定,預(yù)熱器系統(tǒng)無(wú)出現(xiàn)結(jié)皮、堵塞、塌料現(xiàn)象,窯尾燃燒器下移和四級(jí)下料管下移后提高了分解爐的容積,提高了煤粉和物料在分解爐的停留時(shí)間,預(yù)燃器系統(tǒng)熱工工藝更加穩(wěn)定,平均投料量提高10t/h。
(2)脫硝效率及氨水節(jié)約量:
煙氣脫硝窯尾燒成系統(tǒng)優(yōu)化改造后本體濃度大幅度降低,平均NOx本體濃度由原810mg/m3降低至435mg/m3,實(shí)現(xiàn)降低NOx本體濃度46%以上,配合SNCR噴氨系統(tǒng),改造前NOx控制指標(biāo)在100mg/m3以內(nèi);平均氨水用量在1000-1200kg/h;技術(shù)改造后NOx控制指標(biāo)在100mg/m3以內(nèi),平均氨水用量在550-600kg/h;相同NOx控制指標(biāo)下,實(shí)際節(jié)約氨水量在54%左右。
改造后,氨水消耗指標(biāo)同比大幅下降,平均每日日氨水消耗量節(jié)約12噸,全年按300天運(yùn)行時(shí)間計(jì)算,可節(jié)約氨水3600噸,預(yù)計(jì)全年實(shí)現(xiàn)經(jīng)濟(jì)效益252萬(wàn)元以上。
煙氣脫硝窯尾燒成系統(tǒng)優(yōu)化技術(shù)改造前后主要工藝參數(shù)對(duì)比如下:
表2煙氣脫硝窯尾燒成系統(tǒng)優(yōu)化改造前后主要工藝參數(shù)對(duì)比表
主要工藝參數(shù) |
改造前參數(shù)值 |
改造后參數(shù)值 |
頭煤量(t/h) |
12-13 |
12-13 |
尾煤量(t/h) |
20-21 |
20-21 |
臺(tái)時(shí)(t/h) |
370-380 |
380-390 |
二次風(fēng)溫(℃) |
980-1000 |
980-1000 |
三次風(fēng)溫(℃) |
800-900 |
800-900 |
C1出口溫度(℃) |
295-304 |
290-300 |
窯尾溫度(℃) |
1000-1050 |
1000-1050 |
分解爐出口溫度(℃) |
880-900 |
880-900 |
尾煤風(fēng)機(jī)風(fēng)量(m3/min) |
105 |
60 |
尾煤風(fēng)機(jī)風(fēng)壓(KPa) |
28 |
33 |
NOx本體濃度(mg/m3) |
810 |
435 |
NOx控制指標(biāo)(mg/m3) |
150 |
50 |
氨水使用量(kg/h) |
1000-1200 |
750-800 |
熟料KH值 |
0.90-0.93 |
0.90-0.93 |
熟料三天強(qiáng)度(Mpa) |
32 |
32 |
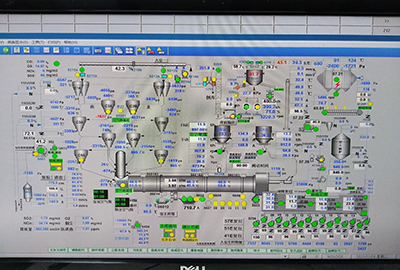
5、結(jié)論
本文通過(guò)對(duì)煙氣脫硝窯尾燒成系統(tǒng)優(yōu)化技術(shù)原理和實(shí)施方案進(jìn)行了詳實(shí)的分析,通過(guò)在山東省某水泥集團(tuán)5000噸熟料生產(chǎn)線的實(shí)踐應(yīng)用,獲得如下結(jié)論:
(1)煙氣脫硝窯尾燒成系統(tǒng)改造通過(guò)優(yōu)化分解爐燃燒器、三次風(fēng)管、四級(jí)下料點(diǎn)在分解爐分布的位置,采用分解爐高強(qiáng)還原燃燒控制技術(shù)可實(shí)現(xiàn)將回轉(zhuǎn)窯內(nèi)熱力型NOx高強(qiáng)還原,大大降低了NOx生成量,可降低NOx本體濃度56%以上。
(2)實(shí)踐證明,煙氣脫硝窯尾燒成系統(tǒng)優(yōu)化技術(shù)改造相對(duì)成熟,也是目前進(jìn)一步降低NOx排放本體濃度節(jié)約氨水用量的有效途徑,采用煙氣脫硝窯尾燒成系統(tǒng)優(yōu)化改造后,相同NOx控制指標(biāo)下,實(shí)際節(jié)約氨水量在58%以上,大大降低了氨水用量和脫硝成本,經(jīng)濟(jì)效益和環(huán)保改善效果明顯。